Leister and Politecnico di Milano present a new 3D printing system that makes it possible to produce large architectural elements
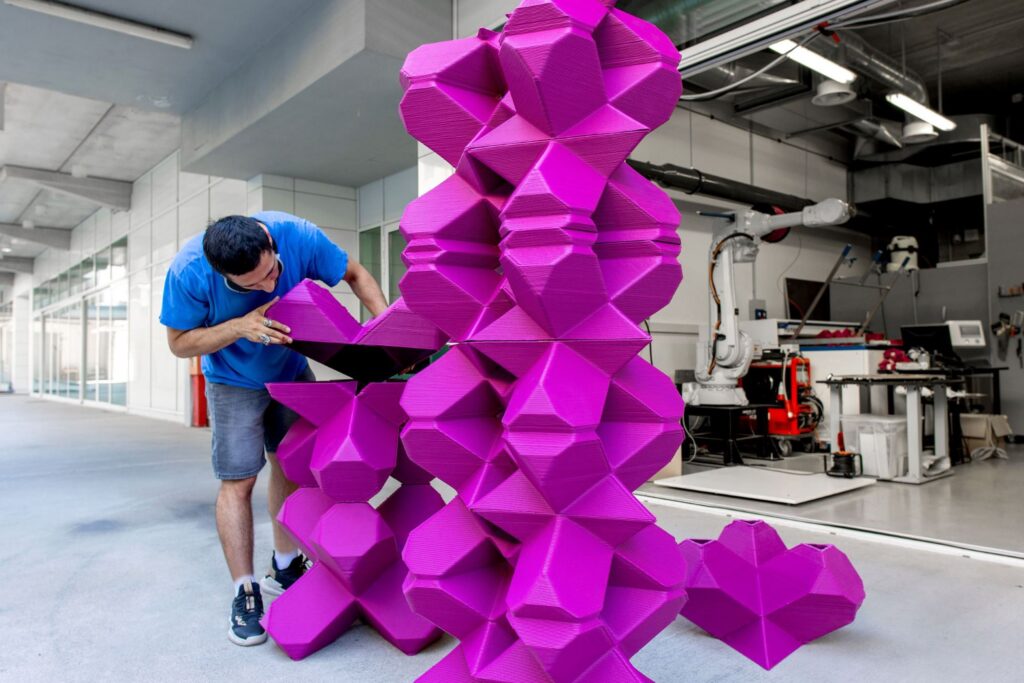
Leister is a Swiss multinational company that designs and manufactures systems for plastic welding and processing. The latter and the Department of Mechanical Engineering of the Politecnico di Milano worked together at the “Cultura Meccanica” project. This initiative resulted in an innovative 3D system that, through the use of the WELDPLAST 600-i extruder, can produce large-scale architectural elements.
Leister and Politecnico di Milano teamed up for the “Cultura Meccanica” project
The science side of the “Cultura Meccanica” project was managed by Prof. Francesco Braghin, Department of Mechanical Engineering, and coordinated by engineer Pierpaolo Ruttico, Department of ABC of (Architecture, Built environment and Construction engineering). Moreover, engineer Carlo Beltracchi directed the work at the INDEXLAB laboratory of the Territorial Center of Lecco with the support of engineer Gabriele Viscardi and computational designer Khalid Alabdula.
The core of the research was the development of techniques for integrating the Leister WELDPLAST 600-i extruder module into an anthropomorphic Fanuc robot to 3D print large plastic elements that are easy to assemble.
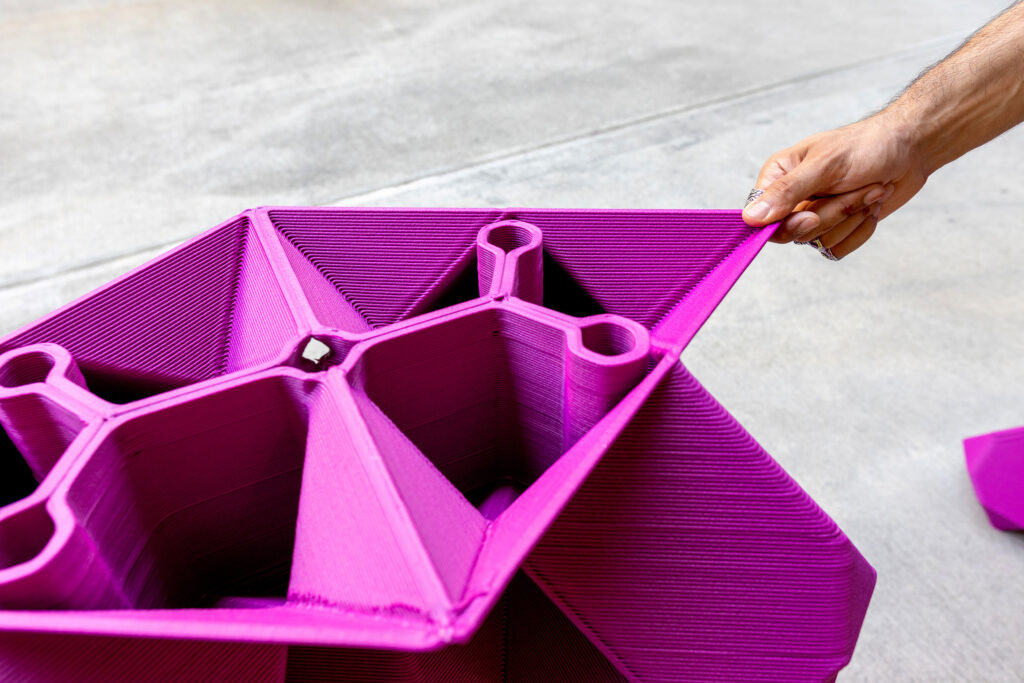
Careful placement and perfect matching of components
With the integration of the extruder into the robot, the various components were carefully placed and perfectly matched. The WELDPLAST’s control computer, power supply and connections were installed directly on the robot’s “wrist” to create a compact, functional and user-friendly plug-and-play system. This arrangement allows for the maximum flexibility of the robot on several axes. It also significantly reduces the risk of cable tangling and possible interference due to the distance between components.
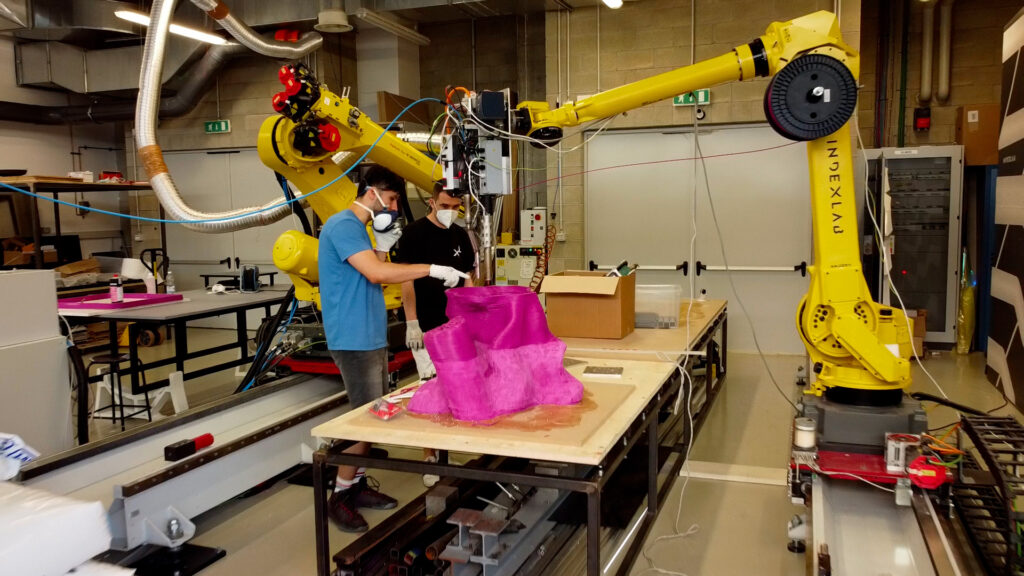
Control via PLC for precise control of the extrusion process
The system developed by Leister and Politecnico di Milano is controlled by a programmable logic controller (PLC). This ensures precise control of the extrusion process and is triggered when the critical temperature for extrusion of the selected material is reached. WELDPLAST 600-i has a printing speed of 50 to 75 mm per second, allowing for the extrusion of up to 3 kg of material per hour in 2.5 kg coils with a diameter of 4 mm.
A successful result
One of the most striking results of this project was to create elements with free forms, both curved and sharp, as well as the ability to create structures with significant protrusions thanks to a specific cutting strategy. This made it possible to overcome the traditional limitations of 3D printing, increasing the range of possible shapes and pushing the boundaries of innovation in additive manufacturing.
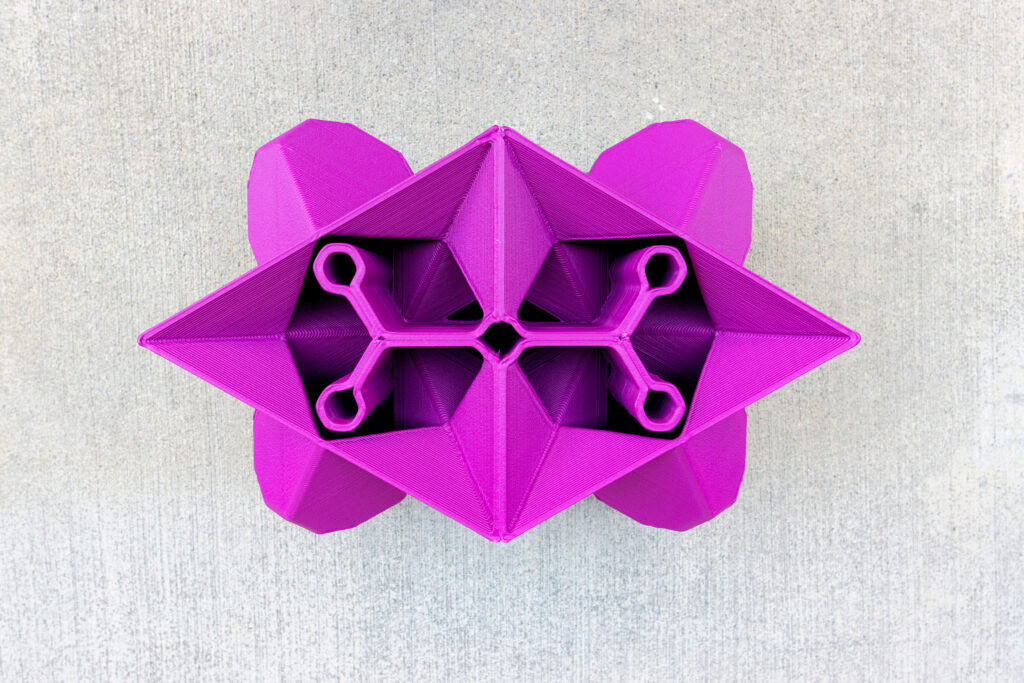
Luigi Vanvitelli’s “Virtù Principesche” in 3D printed version
With this new 3D printing process, the Department of Mechanical Engineering of the Politecnico di Milano collaborated with the Milan-based art studio Cracking Art to reproduce Virtù Principesche by architect Luigi Vanvitelli.
The Fanuc anthropomorphic robotic arm with six mechanical joints used the WELDPLAST 600-i extruder to deposit a polymer material layer by layer relying on an algorithm that converted the 3D models into motion commands. This additive manufacturing process is repeatable but created unique pieces, combining art with advanced technology.
New horizons for architectural design
Computational designer Khalid Alabdula has been researching “discrete architecture”. His research focuses on components that are 3D printed to configure architectural structures. This innovative approach uses polypropylene reinforced with glass fibers and offers new possibilities in the field of architectural design.
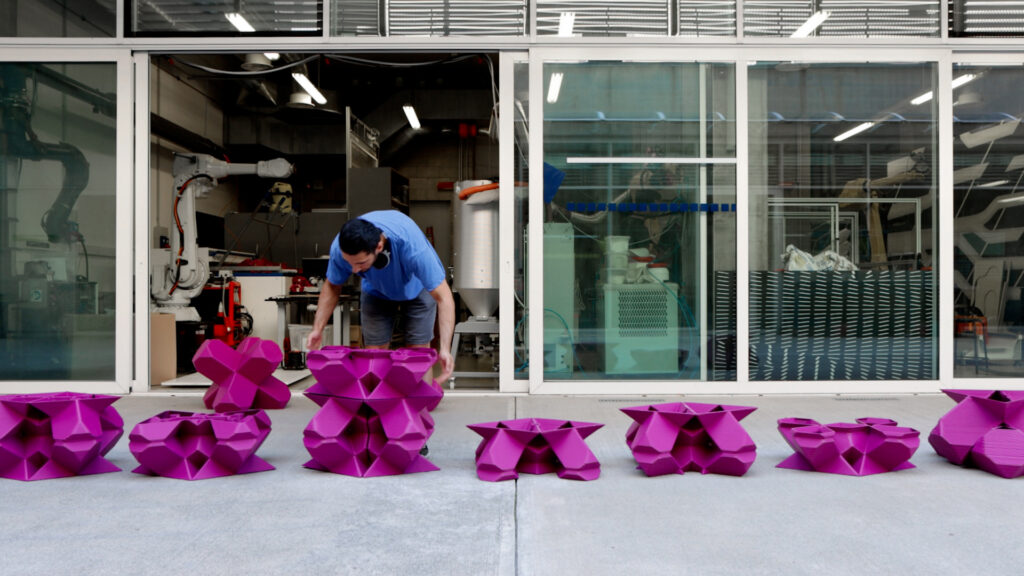